The Science Behind Porosity: A Comprehensive Overview for Welders and Fabricators
Understanding the elaborate mechanisms behind porosity in welding is essential for welders and producers pursuing remarkable craftsmanship. As metalworkers explore the midsts of this sensation, they uncover a globe regulated by different factors that influence the formation of these minuscule spaces within welds. From the make-up of the base materials to the ins and outs of the welding process itself, a wide variety of variables conspire to either intensify or reduce the existence of porosity. In this comprehensive overview, we will unwind the science behind porosity, discovering its effects on weld quality and unveiling advanced methods for its control. Join us on this journey through the microcosm of welding flaws, where accuracy fulfills understanding in the search of flawless welds.
Recognizing Porosity in Welding
FIRST SENTENCE:
Evaluation of porosity in welding reveals critical understandings into the honesty and top quality of the weld joint. Porosity, identified by the visibility of tooth cavities or gaps within the weld steel, is a typical worry in welding procedures. These gaps, if not appropriately resolved, can jeopardize the architectural stability and mechanical homes of the weld, causing possible failures in the completed product.
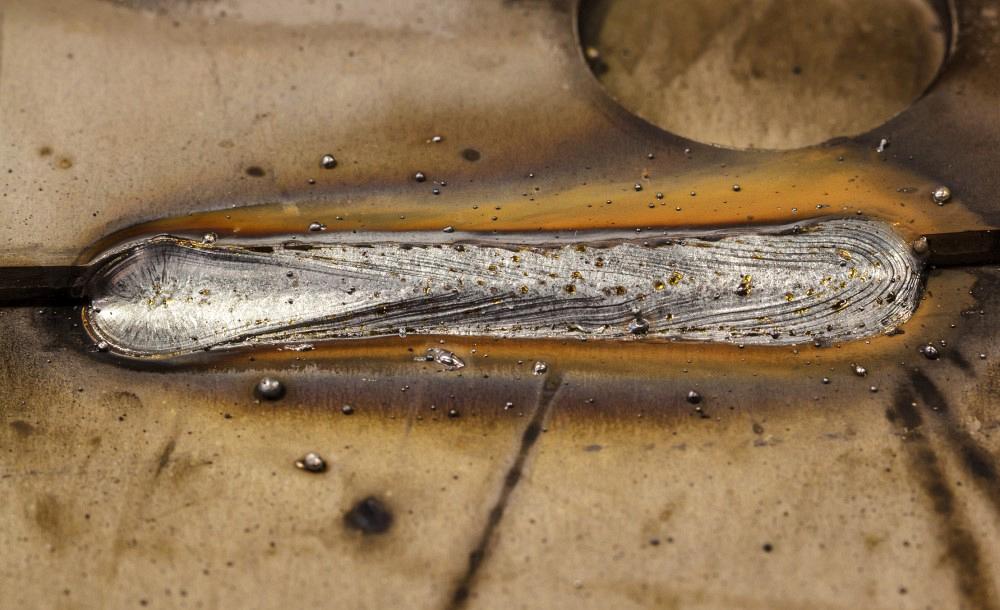
To spot and measure porosity, non-destructive screening techniques such as ultrasonic screening or X-ray inspection are usually used. These methods enable the identification of inner issues without compromising the integrity of the weld. By assessing the dimension, shape, and distribution of porosity within a weld, welders can make educated decisions to enhance their welding processes and attain sounder weld joints.
Variables Influencing Porosity Development
The incident of porosity in welding is affected by a myriad of factors, varying from gas securing performance to the details of welding specification setups. Welding parameters, consisting of voltage, current, take a trip speed, and electrode type, likewise impact porosity development. The welding technique utilized, such as gas metal arc welding (GMAW) or secured steel arc welding (SMAW), can affect porosity formation due to variations in warm distribution and gas coverage - What is Porosity.
Results of Porosity on Weld Quality
Porosity development considerably jeopardizes the structural honesty and mechanical residential or commercial properties of bonded joints. When porosity exists in a weld, it develops gaps or dental caries within the product, decreasing the general strength of the joint. These spaces function as anxiety concentration points, making the weld more prone to splitting and failing under tons. The visibility of porosity likewise compromises the weld's resistance to deterioration, as the caught air or gases within deep spaces can respond with the surrounding setting, leading to degradation in time. Furthermore, porosity can hinder the weld's capacity to withstand stress or influence, further threatening the general quality and dependability of the bonded structure. In important applications such explanation as aerospace, auto, or architectural building and constructions, where security and durability are paramount, the detrimental effects of porosity on weld top quality can have severe effects, stressing the value of decreasing porosity through appropriate welding methods and treatments.
Methods to Minimize Porosity
To boost the high quality of bonded joints and guarantee structural stability, welders and producers employ specific strategies focused on minimizing the development of gaps and dental caries within the material during the welding process. One effective technique to minimize porosity is to make certain correct material preparation. This consists of extensive cleansing of the base steel to remove any kind of contaminants such as oil, oil, or moisture that could contribute to click porosity formation. In addition, using the ideal welding specifications, such as the right voltage, current, and travel speed, is crucial in protecting against porosity. Preserving a regular arc length and angle throughout welding also helps in reducing the chance of porosity.

Moreover, picking the appropriate shielding gas and keeping proper gas flow prices are vital in reducing porosity. Making use of the appropriate welding strategy, such as back-stepping or employing a weaving activity, can also assist disperse warm uniformly and decrease the chances of porosity formation. Last but not least, making sure correct ventilation in the welding atmosphere to remove any possible resources of contamination is vital for accomplishing porosity-free welds. By applying these techniques, welders can effectively minimize porosity and produce high-grade welded joints.

Advanced Solutions for Porosity Control
Applying cutting-edge modern technologies and innovative techniques plays a pivotal duty in attaining premium control over porosity in welding processes. One sophisticated option is making use of advanced gas blends. Protecting gases like helium or a mix of argon and hydrogen click can help in reducing porosity by giving far better arc stability and boosted gas coverage. Furthermore, employing innovative welding techniques such as pulsed MIG welding or modified atmosphere welding can also aid mitigate porosity problems.
One more sophisticated solution includes making use of sophisticated welding devices. Utilizing tools with built-in functions like waveform control and sophisticated power resources can boost weld top quality and decrease porosity risks. The implementation of automated welding systems with precise control over specifications can considerably decrease porosity flaws.
Moreover, incorporating innovative tracking and inspection innovations such as real-time X-ray imaging or automated ultrasonic screening can assist in spotting porosity early in the welding process, allowing for immediate rehabilitative activities. On the whole, integrating these sophisticated services can significantly enhance porosity control and boost the overall top quality of bonded components.
Conclusion
To conclude, recognizing the scientific research behind porosity in welding is crucial for welders and producers to create premium welds. By determining the elements influencing porosity development and executing strategies to lessen it, welders can enhance the overall weld quality. Advanced remedies for porosity control can even more improve the welding procedure and ensure a strong and trustworthy weld. It is essential for welders to continually educate themselves on porosity and execute finest methods to attain optimal results.
Comments on “What is Porosity in Welding: Best Practices for Avoiding Permeable Welds”